The Science Behind Rigid Stranders and Cable Quality Control: Ensuring Excellence in Electrical Manufacturing
Release time:
2025-02-16
Rigid strander for Power Cables are specialized machines used in the production of twisted strands of wire
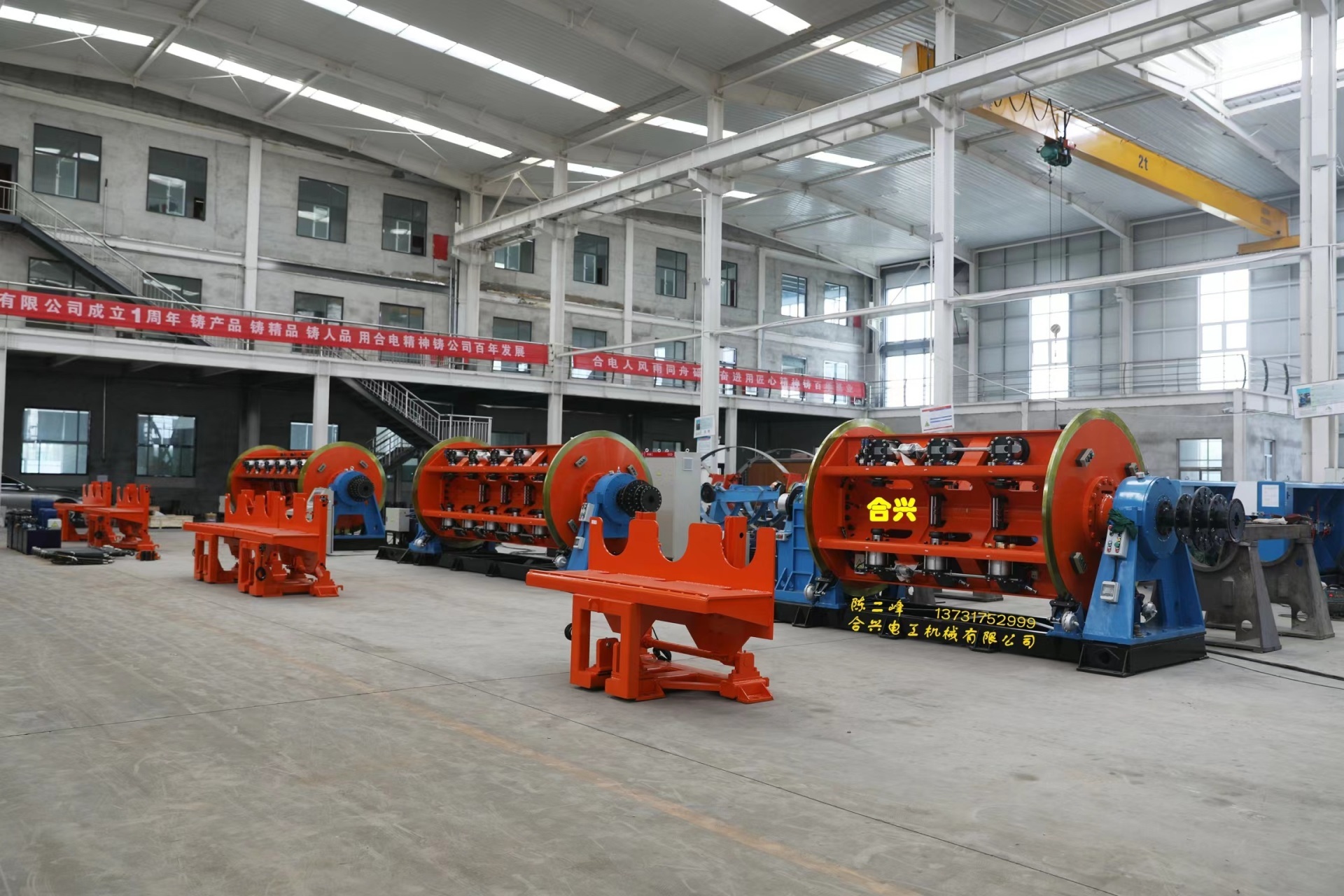
In the rapidly evolving field of electrical manufacturing, rigid strander for power cables has emerged as crucial machinery for producing high-quality cables. These devices are designed to efficiently bundle multiple strands of wire into a single cable, ensuring it meets strict industry standards. Understanding the underlying science of rigid stranders is essential for manufacturers aiming to optimize their production processes and enhance the overall quality of their electrical products.
The Importance of Cable Quality Control
Quality control in cable manufacturing is not merely a regulatory requirement; it is a commitment to safety and performance. High-quality cables ensure reliable electrical transmission, reduce the risk of failures, and enhance the longevity of the end products. Implementing robust quality control measures throughout the manufacturing process is essential for achieving these goals.
What Are Rigid Stranders?
Rigid strander for Power Cables are specialized machines used in the production of twisted strands of wire. They play a vital role in creating various types of cables, including power cables, communication cables, and specialty cables for unique applications. By using rigid stranders, manufacturers can produce cables that are not only strong and flexible but also capable of withstanding environmental stressors.
How Rigid Stranders Operate
Rigid stranders function by utilizing a series of rotating spools that draw wire strands and twist them together. This process can be fine-tuned to produce different stranding configurations, which directly affects the cable's flexibility and strength. The precision offered by modern rigid stranders allows manufacturers to maintain consistent quality throughout the production cycle.
Key Components of Rigid Stranders
The efficiency of rigid stranders relies on several key components:
- Spools: These hold the individual wire strands that will be twisted together.
- Twisting Mechanism: This component ensures that the wires are twisted at the correct tension and angle, critical for cable performance.
- Control System: Advanced control systems allow operators to monitor and adjust the machine settings in real-time, ensuring optimal performance.
Enhancing Cable Quality Through Advanced Stranding Techniques
The evolution of stranding technology has revolutionized cable manufacturing. By adopting advanced techniques, manufacturers can enhance cable quality and performance dramatically.
Innovative Stranding Methods
One of the most significant advancements in stranding technology is the introduction of compact stranding. This method reduces the overall size of the cable while maintaining its strength and flexibility. This is particularly beneficial for applications where space is limited.
Benefits of Compact Stranding
- Reduced Weight: Lighter cables are easier to handle and install.
- Improved Flexibility: Compact stranded cables offer superior flexibility, making them ideal for dynamic applications.
- Enhanced Performance: The tight packing of strands improves electrical performance by reducing resistance and enhancing signal integrity.
Quality Control Measures in Cable Manufacturing
Implementing effective quality control measures is paramount to producing high-quality cables. These measures encompass various stages of the manufacturing process.
Inspection and Testing Procedures
Regular inspections and testing of cables during production ensure they meet established standards. Key procedures include:
- Visual Inspections: Checking for physical defects such as kinks, breaks, or improper stranding.
- Electrical Testing: Verifying that cables meet electrical conductivity and insulation resistance specifications.
- Mechanical Testing: Assessing the tensile strength and flexibility of the cables to ensure they can withstand the required operating conditions.
The Role of Automation in Quality Control
Automation plays a pivotal role in enhancing quality control processes. Automated systems can monitor production parameters in real-time, allowing for immediate adjustments to maintain quality standards. This not only increases efficiency but also reduces the likelihood of human error.
The Science of Materials Used in Cable Manufacturing
The materials chosen for cable manufacturing significantly impact the overall quality and performance of the final product.
Common Materials in Cable Production
- Copper: Known for its excellent electrical conductivity, copper is the most commonly used material in electrical cables.
- Aluminum: A lighter alternative to copper, aluminum is often used in applications where weight reduction is critical.
- Insulation Materials: Various polymers and compounds are employed to insulate cables, protecting them from environmental factors and ensuring safety.
Material Selection and Quality Control
The selection of materials must align with the intended application of the cable. Rigorous testing of materials, including tensile strength and thermal stability, ensures that only high-quality inputs are used in production.
Regulatory Standards and Compliance in Cable Manufacturing
Adhering to regulatory standards is a critical aspect of cable manufacturing. Various organizations establish guidelines that manufacturers must follow to ensure that their products are safe and reliable.
International Standards for Cable Quality
Organizations such as the International Electrotechnical Commission (IEC) and Underwriters Laboratories (UL) set standards for cable quality and safety. Meeting these standards not only enhances product reliability but also builds consumer trust.
Benefits of Compliance
- Market Access: Compliance with international standards opens up new markets for manufacturers.
- Customer Confidence: Adhering to recognized standards builds confidence among consumers and business partners.
- Risk Reduction: Ensures that products are tested for safety and performance, reducing the risk of failures and recalls.
Future Trends in Rigid Stranding Technology
The landscape of cable manufacturing is continually evolving. Emerging technologies and trends promise to reshape the industry further.
Smart Manufacturing and Industry 4.0
The integration of Industry 4.0 principles is transforming cable manufacturing. Smart manufacturing technologies, including the Internet of Things (IoT) and data analytics, enhance production efficiency and quality control.
Benefits of Smart Manufacturing
- Real-time Monitoring: Enhanced data collection and analysis allow for proactive adjustments to production processes.
- Predictive Maintenance: IoT devices can predict when machines need maintenance, reducing downtime and improving productivity.
- Customization: Real-time data helps manufacturers quickly adapt to changing market demands and customer preferences.
Conclusion
The science behind rigid stranders and cable quality control is a complex yet fascinating field that plays a vital role in electrical manufacturing. By understanding the intricacies of rigid stranders, implementing robust quality control measures, and staying ahead of industry trends, manufacturers can produce high-quality cables that meet the demands of an ever-evolving market. Investing in advanced technology and adhering to regulatory standards will ensure that your products not only perform well but also establish a strong reputation for reliability and safety in the electrical industry.
TAG:
Recommend News
HEXING CABLE MACHINERY
TEL: +86-317-3601666, +86-317-3236119
FAX: +86-317-3618408
E-MAIL: china@hbhxdg.cn
E-MAIL: hbhxdg@gmail.com
WEB: http://www.hbhxdg.cn
ADD: Baoantun Industrial Zone, Hejian City, Hebei Province